Garda Carbon Lab is equipped with the best equipment for the design, production and geometric or structural analysis of carbon fiber components:
Laminating
Clean Room ISO 8
- 150m2
- Temperature and Humidity control
- ISO 8 certified



Fabric Cutting
1x Numerical control cutting plotter with multiple tools (1.8 m wide, rotating belt) located in temperature and humidity controlled room
Laminating area
- 200 m2 designated for pre-impregnated lamination of large-sized components (outside the clean room)

Tooling/Milling
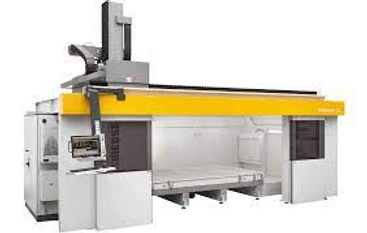

5 Axis mill
5 Axis Milling Machine (4m x 2m x 1.2m) → Milling machine dedicated to the milling of models or molds in resins or light alloys or to the milling or trimming of composite materials.
-
3 Axis vertical mill
Doosan 3-axis Vertical Mill (1020mm x 540mm x 510mm) → Dedicated to the milling of molds or components in light alloys, steels and other super alloys.
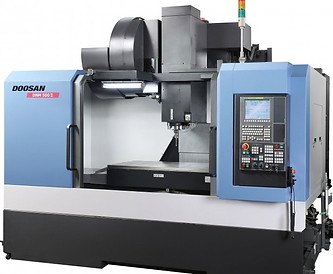
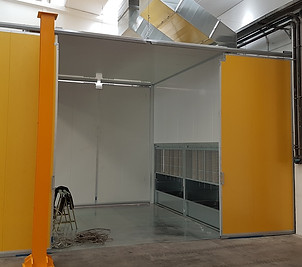

Trimming/bonding Booth
~70m2 Area dedicated to the bonding of components and to the lamination of dry fabrics.
- Trimming booth (5m x 4m) with dust extraction.
Curing
Ovens/Autoclaves
- 1x Autoclave 4500 x Ø2000 mm (225°C @ 15 bar)
- 1x Composite polymerization oven with data logging
(8500x6500x1500 mm @ 130°C)
- 1x Composite polymerization oven with data logging
(2000x700x700 mm @ 220°C)
- Each oven has the ability to monitor and record vacuum and/or pressure levels to provide the customer with a further guarantee.

QC



QC - Quality Control
- x1 3D Scanner Accuracy 0.025mm → dedicated to reverse engineering processes and geometric tolerance control
- x1 Ultrasonic Scanner 5 Hz to 6000 Hz to certify the structural integrity of finished components